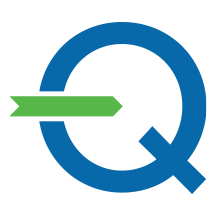
We're recognizing 10 employees who have earned belt certifications and completed NEXT and Just Do It projects.
CLASS Belt Certifications
- Yellow Belt: Jim Bennett (Gas Transmission & Distribution) – Optimize Welding Services
- Yellow Belt: Gillian Marks (Environmental) – Lab Equipment Training
- Advanced Yellow Belt: Steve Berube (Water Production & Distribution) – Maintenance Relief Operator Scheduling
Left to right: Jim Bennett, Gillian Marks, Steve Berube
NEXT/Innovation Projects
NEXT is an acronym for iNnovation EXcellence Team, which was formed as a result of the strategic planning process in fiscal year 2020. The purpose of NEXT is to help employees not simply improve processes but to entirely change processes through innovative thinking.
An idea is considered innovative when a new process is established or a change to an existing process is made independent of continuous improvement tools and provides measurable benefits to the Trust. If you have an innovative idea, Quality has a process to help you evaluate and implement it. Visit the Improvement Ideas List to submit your idea for Quality review. All completed CLASS and NEXT/Innovation projects can be found on Quality's Completed Projects Page.
- Tracey Black (Underground Engineering & Construction) – Envirocure Product Review (pictured at right)
- Roger Hanas (Wastewater Collections) – Manhole Lid Tool
Just Do It Projects
A Just Do It project is a great way to continuously improve something where the solution is already known. This doesn't mean it necessarily has to be a quick or simple project; it just doesn't go through the Define, Measure, Analyze, Improve, and Control process. Just Do It projects can make a big impact on efficiency and savings. All completed Just Do It projects can be found on Quality’s CI Activities and Completed Projects page.
- Anthony Miller (Wastewater Plant Operations) – Chain of Custody Form Changes
- Randy Rollins (Billing & Customer Service) – Spanish Queue
- Paula Birdsong (Shared Field Services) – Electronic Time Sheets
- Dan Kramer (Plant Engineering) – Southport Scum Line Improvements
- Michelle Dinkins (Information Technology) – IT Support for Service Providers
Mid-Year Reminder: Strategic Initiative 60
Per Strategic Initiative 60, all divisions and departments are to define their top three to five critical processes and conduct a gap analysis to develop a list of procedures that require documentation.
In fiscal year 2021, all items listed below, at minimum, were to be documented on the standard template available on Quality’s iTrust site:
- Identify and document your department’s critical processes (a minimum of three).
- List all procedures and sub-processes.
- Conduct a gap analysis to determine what documentation exists (or doesn’t exist) for each procedure and sub-process, and any actions needed to review or update.
- Tip: Consider using Gemba Walks to review procedures and sub-processes and associated documentation.
In fiscal year 2022, plans should be executed to achieve current and accurate documentation as explained below:
- Where documentation exists: Review, verify, and validate current documentation
- Where documentation doesn’t exist: Create process maps, work instructions, etc.
Send Project Benefits to Quality
Have you recently completed a CI project that has resulted in measurable benefits (e.g., saving time and/or money, increasing revenue)? If so, please contact a member of the Quality team so they can add the results of your project to the Benefits Dashboard.
Calling Leaders Interested in Earning a Blue Belt
The Citizens Lean Leadership training and certification program provides leaders (i.e., supervisors, managers, and directors) the opportunity to discuss leadership tools, struggles, and ideas while creating a common approach for supporting and leading lean thinking. Quality plans to conduct a session in August. Please reach out to Quality or your CLASS Ambassador if you are interested in participating.