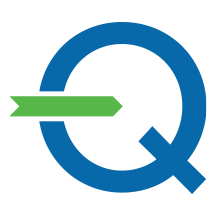
What is a Gemba Walk?
Going to the Gemba, also known as “the real place” where work is done, is an important component of a Lean organization. A Gemba Walk allows leaders to “go and see” processes personally, with the people doing the work, so they can understand and ask questions. This fosters a collaborative environment in which to discover problems or wastes and develop action plans to correct them.
Gemba Walk training is available by contacting the Quality department and is designed to provide leaders with the understanding of what a Gemba Walk is (and is not) and how to conduct one in their area. A Gemba Walk is not a random walk around to look for problems, an exercise in being seen or making a management presence visible, or another way to audit a process. Gemba Walks can be conducted by leaders at all levels of the organization, with the intent of learning about a particular process. Benefits include building trust and relationships; allowing time for face-to-face communication; uncovering problems; increasing employee engagement and development; and developing a Lean culture. The Gemba Walk template should be used to document follow-up items with accountability and dates, as well as to communicate decisions and/or improvements made.
What Makes a CLASS Project?
A Citizens Lean and Six Sigma (CLASS) project starts with a clear problem statement and uses Lean/Six Sigma to arrive at a solution with a measurable benefit.
- The problem statement should be clear, and the solution should directly address the problem with a measurable improvement
- Lean/Six Sigma projects use a Define, Measure, Analyze, Improve, and Control (DMAIC) process and can be completed at several levels based on the complexity of the tools used. These include Yellow Belt, Advanced Yellow Belt, Green Belt, and Black Belt. Quality can provide training and mentoring.
- Just Do It (JDI) projects are a process improvement applied to correct problems when the solution is generally known. There must be a measurable improvement (e.g., errors reduced, reduction in process steps by removing decision points or hand-offs).
- All belt projects and JDIs must be documented on forms provided by Quality.
Examples of Good Business Practices But Not CLASS Projects
- A business analysis to determine if resources should be insourced or outsourced, return on investment decisions
- An ad hoc process/communication correction or billing correction
- Changes to a process because of regulations or compliance
- System maintenance (e.g., version or technology upgrade)
- Purchasing decisions based on value, vendor evaluation, etc.
- Organizing and cleaning up a workspace or work files; that should be documented as a 6S project instead
- A process improvement without a measurable benefit
- An audit or survey that does not result in a process improvement
- Changes to a spreadsheet or report (unless associated with a project)