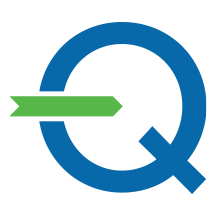
Employees can now add CLASS-related goals, from participating in Continuous Improvement (CI) events and documentation to earning a belt certification, to their Individual Development Plan. In this issue, we're also recognizing 10 employees for recently completing CI projects.
Continuous Improvement (CI) Goals Available in CSA PerformanceCLASS-related goals are now available in the goal library in CSA Performance! As you create your Individual Development Plan, consider one of the CI goals listed below. If you would like to talk through additional or more specific goals, reach out to any member of the Quality Systems team.
- Continuous Improvement Participation: CI activity may include completing a Just Do It project, creating process documentation, completing a sustained 6S event, creating a Knowledge Transfer Plan, conducting an After-Action Review, or conducting a Root Cause Analysis event. Documentation requirements can be found in the Levels of Quality Quick Reference Guide, which is accessible by clicking the “CI Tools & Templates” button on the Quality iTrust site.
- Obtain a CLASS Belt: This includes Yellow, Advanced Yellow, Green, Black, or Blue Belts. As applicable, attend training facilitated by Quality, lead and complete an improvement project, and utilize the A3 form and other CI tools.
- Complete a NEXT (Innovation) Project: Lead and complete either an Innovation project or a product review and use Quality’s A3 form to document the project.
- Conduct a Gemba Walk: Area leadership observes and documents the Gemba walk using Quality’s template. Complete all follow-up action items.
CLASS Belt Certification
Nick Polley (Gas Distribution & Transmission) - Yellow Belt
- Gas Operations Work Planning: Nick’s project improved efficiencies for the eight crews that maintain the underground gas infrastructure for Marion County and Westfield and respond to gas emergencies. Microsoft Teams was deployed for better collaboration, and route changes have led to a reduction in mileage, which has led to cost savings as well.
iNnovation EXcellence Team (NEXT)
Justin Burnett (Underground Engineering & Construction)
Master Meter Ultrasonic Water Meter Evaluation - Product Review: Justin conducted a life cycle cost analysis to compare the costs of meters, testing, and repairs in an effort to reduce meter accuracy loss and the number of water meter repairs over time.
Just Do It Projects
A Just Do It is a project for which the cause and solution are already known. This doesn’t mean the project is necessarily quick or simple, but rather that it doesn’t need to go through the Define, Measure, Analyze, Improve, and Control process. These projects can make a big difference in efficiency and savings. Several employees have completed Just Do It projects already in fiscal year 2022:
- Stephanie Tuvell (Energy Distribution Engineering) - Construction Orders
- Jennifer Velikan (Information Technology) - Revenue Assurance Analytics
- Richard Jones (Information Technology) - Support Center Call Back Queue Option
- Carla Baber (Information Technology) - Single Sign-On Kiosks for Maintenance Reports
- Garrick Hardy (Information Technology) - Employee ID Search Tool
- Deb Foster (Treasury) - Purging Prior Years’ Registers
- Dustin Abramson (Wastewater Plant Operations) - Valve Labels
- Wastewater Plant Operations Team - Baseline Report
You can now view all Completed A3s, Just Do It projects, and 6S Events on Quality’s new CI Activities and Completed Projects page.