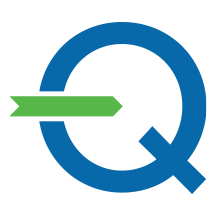
Along with completing more than a dozen recent Just Do It Projects, employees continue to earn Yellow Belt certifications and complete Innovation projects.
CLASS Belt Certification – Yellow Belt
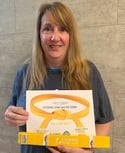
- Carol Traylor (Billing & Customer Service): Contact Center Rep Call Monitoring - pictured at left
Innovation Projects
An idea is considered innovative when a change to an existing process or a newly established process provides measurable benefits to the Trust independent of continuous improvement tools. Quality has a process to help you evaluate and implement your innovative idea; visit the Improvement Ideas List to submit it for review. All completed CLASS and Innovation (NEXT) projects can be found on Quality's Completed Projects page.
- Brittany Meunier & Tom Laue (Energy Distribution Engineering): Gas Patrolling and Locate Verification Program
Just Do It Projects
A Just Do It project is a great way to continuously improve something where the solution is already known. This doesn't mean it has to be a quick or simple project; it just doesn't go through the Define, Measure, Analyze, Improve, and Control (DMAIC) process. Just Do It projects can still make a big impact on efficiency and savings. All completed Just Do It projects can be found on Quality’s CI Activities and Completed Projects page.
- John Meehan (Billing & Customer Service): C2M Training Updates
- Madison Barker (Energy Distribution Engineering): Scanning Maps with the Plotter
- Stephanie Tuvell (Energy Distribution Engineering): Turning In Control Prints
- Angela Guynn (Human Resources): Direct Deposit
- Dennis Claffey (Shared Field Services): Route Sheets
- Dennis Claffey (Shared Field Services): New Meter Readers in Active Directory
- Kris Lang (Supply Chain): Auto Approval – Delivery Date Changes
- Susan Unversaw (Supply Chain): Certificate of Insurance File Clean Up
- Ronald Delph (Thermal): Softener Overhauls – Perry K Plant
- Brian Tyler (Thermal): Gas Detector Calibrations
- Del Morris (Thermal): Steam Distribution Utilize Spoils Pile – Langsdale
- Jennifer Bailey (Treasury): Due Diligence Calls
- Paul Grocki (Treasury): Insurance Related FAQs
- Joni Staten (Wastewater Plant Operations): Preventative Maintenance Optimization
- Chris Kennedy (Wastewater Plant Operations): Eagle Creek Dam Data Entry
Process Documentation
Process documentation ensures that processes are clear, repeatable, and effective. After (or while) documenting a process, look for opportunities to apply lean principles and remove unnecessary or non-value-added steps. Clear and complete process documentation is critical for knowledge transfer. The CI Tools and Templates page has a Work Instructions template in the Continuous Improvement section. Process documentation and Knowledge Transfer Plans will earn credit for the FY22 Levels of Quality as Commitment to Continuous Improvement. See your CLASS Ambassador or any member of the Quality team if you have questions.