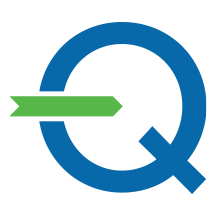
Continuous improvement is still moving forward – even remotely in some cases! The following employees completed training on the use of continuous improvement tools and documentation and completed a project to receive certification.
Yellow Belt Certifications (pictured below, left to right, top to bottom)
Don McCann (Plant Engineering) – Fleet Specifications
Joe Turnquist (Program & Technical Services) – Asset-in-service Data Collection
Jim McLaughlin (Billing & Customer Service) – Temporary Hydrant Meter Information
Staci Lewis (Quality) – Temporary Hydrant Meter Pick Up/Bill Collection Process
Tracy Webster (Information Technology) – Disaster Recovery Site
Melissa Lawson (Shared Field Services) – Water Meter Warranty Tracking
Dustin Reed (Water Production) – Stream/Interstate Crossing Inspection Optimization
Mike Elliott (Water Distribution) – H2O To Go Mobile Water Trailer Program
Advanced Yellow Belt Certifications (pictured below, left to right)
Dan Kramer (Plant Engineering) – GBT Polymer System Improvements
Katie Gomes (Shared Field Services) – USS Recap Sheets
Green Belt Certifications
We recently certified several Green Belt projects. Green Belt training consists of three days of instruction on continuous improvement tools that builds upon the initial Yellow Belt training. The projects will have a higher level of data analysis and typically result in greater financial savings (the goal is $25,000 or more).
Katie Gomes (Shared Field Services) – Water Meter Trends: Shared Field Services will avoid pulling 9,500 water meters annually. Previously, all water meters pulled were tested. Now, meters not needed for IURC or warranty testing are not tested, reducing tested meters by 4,000 annually using the 2019 baseline. These changes will lead to a savings of $1.2 million ($915,000 in FY20), which will offset the projected increase expense required to pull and test 3,000 more meters for IURC compliance. This project also improved the integrity of all water meter reporting data. (Pictured above)
Madison Barker (Energy Distribution Engineering) – Staging Area Backordering: A standard electronic form and a backordered report was created for use in ordering supplies for the Miller Pipeline staging area at Belmont. The form ensures ordering quantities are correct, removes manual ordering paperwork, and gives visibility to the ordering and receiving process, reducing time and errors. The backordered report eliminates over-ordering of parts that are out of stock. The savings are not yet quantified.
Chris Kennedy (Wastewater Operations) – Air Nitrification System (ANS) Contact Stabilization Optimization This project implemented a solution that adjusts the Maximum Allowable Blowers and Dissolved Oxygen levels during contact stabilization events, which were responsible for 36 peak energy demand intervals in 2019. The solution will reduce the intervals, saving around $100,000 annually.